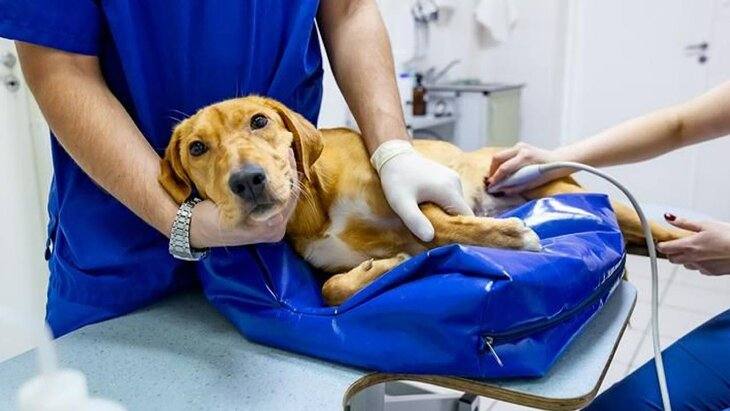
В контакт-центре госветслужбы столицы появился новый номер
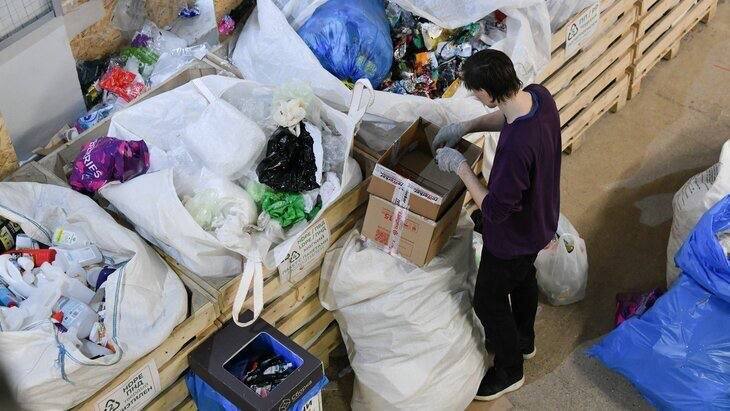
1,2 млн тонн вторсырья собрали в столице за 9 месяцев 2024 г.
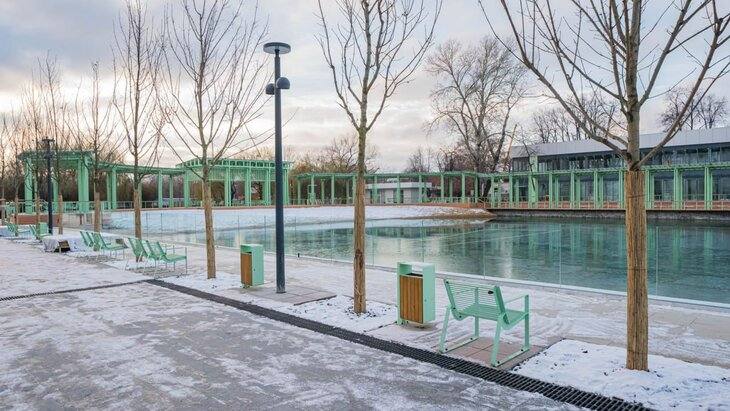
В столице высадят порядка 90 тыс. деревьев
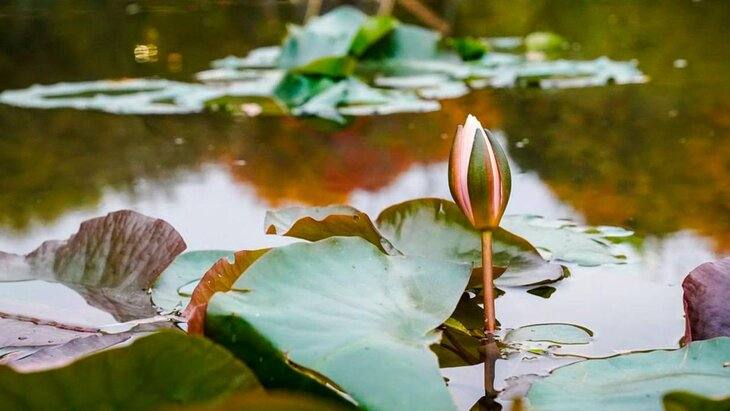
Завершена реабилитация 2-го Николо-Хованского в ТиНАО
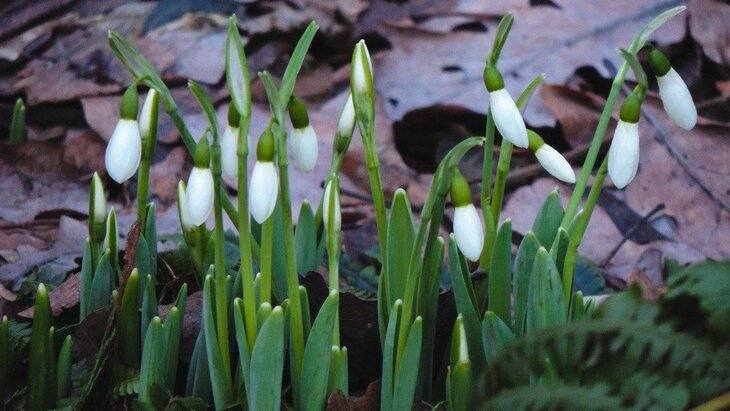
Департамент природы столицы объяснил цветение первоцветов
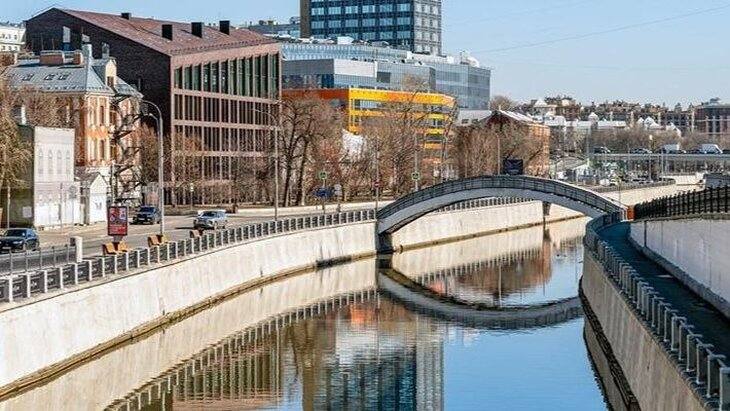
700 деревьев высадят на набережных Яузы
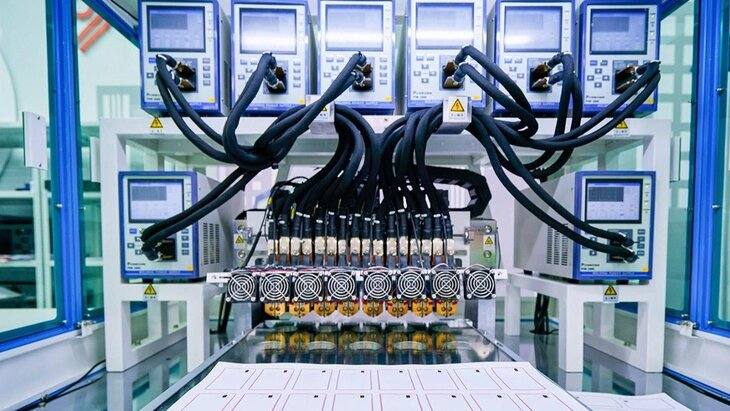
В 2 раза вырос оборот высокотехнологичных производств столицы
Повышена "выносливость" газотурбинных двигателей российского производства
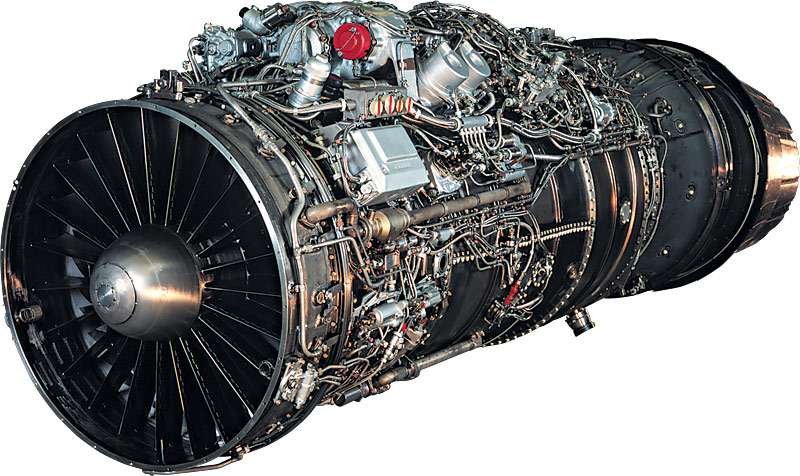
Как сообщил информационный портал Metallinfo, прошли успешные испытания абсолютно нового связующего материала «алюмокс». Он разработан учеными для производства авиационных двигателей. Проводили испытания Московский авиационный институт и НЦП «Салют».
Материал необходим для изготовления лопаток, работающих в газотурбинных двигателях.
По мнению специалистов, новая уникальная разработка позволит улучшить технологию отлива лопаток. Это продлит срок службы двигателей и усовершенствует их эксплуатационные качества.
Виталий Клочков, директор НЦП «Салют» рассказал, что новый материал удовлетворяет потребности снижения массы и повышения тяги двигателей.
Ранее разработанная технология изготовления лопаток из никелиевых сплавов, исчерпала все ресурсы развития. Требуются новые материалы, способные выдерживать повышения температурного режима до 1800 градусов. Чтобы получить такие материалы, необходимо использовать тугоплавкие оксиды иттрия, цирконий.
В разработанной технологии используется безкремнеземистый алюмокс, как связующий элемент. Получили его на основе алиминий-органических соединений.
Металлографические исследования лопаток показали, что новый материал отвечает поставленным целям, обеспечивает изделию требуемые эксплуатационные характеристики. В 7 раз снижено отрицательное влияние на процесс формовки лопаток взаимодействия между формой и металлом заготовки. Форма для отливки теперь имеет свойства большей теплопроводности, чем из этилсиликата.
Изменения в оборудовании при использовании нового материала будут минимальны и не потребуют серьезных затрат. Это также важное достижение разработчиков.